Behind the scenes with Galfer | Glowing discs and high tech
On a recent press trip to try out some new brake pads, Visordown got the chance to go behind the scenes at the Galfer factory
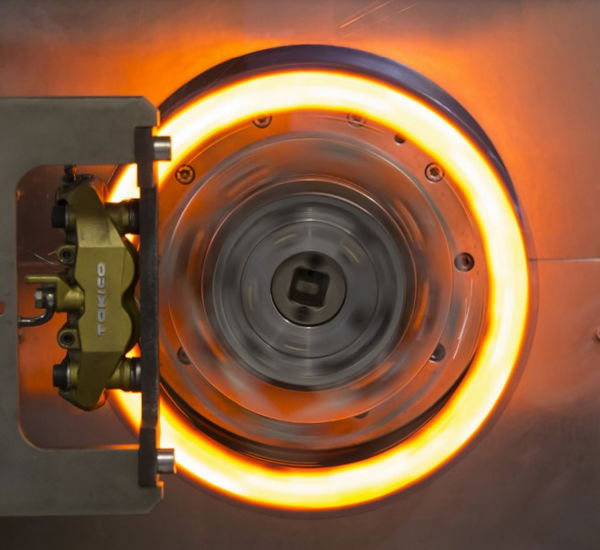
BARCELONA, home to the Circuit de Catalunya, le Sagrada Família, and renowned braking component manufacturer Galfer, which is celebrating its 70th anniversary this year.
At a recent press trip to check out the firm's new G1310 pads and Floatech discs, the good people at the head office gave me the chance to have a mooch around the factory for a behind-the-scenes look at how they work. Being the nosy so-and-so I am, I naturally agreed and spent an afternoon taking in the sights and sounds of their high-tech facility.
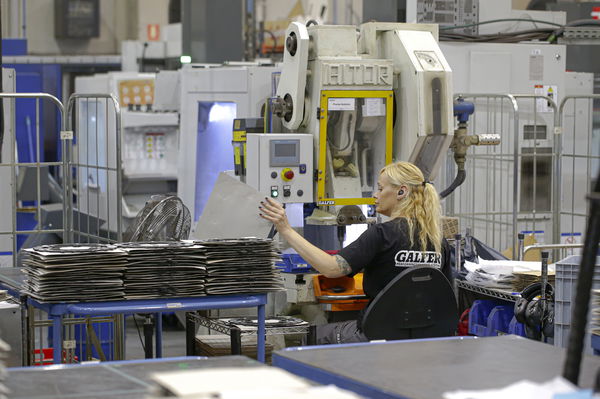
Galfer Performance Braking Systems factory tour
The first thing that hits you as you leave the swish, airconditioned head office and down into the bowels of the factory is the heat. With the outside temperature in the thirties, and all these lasers and ovens doing their thing, the factory floor is no place for someone scared of a little heat – fair play to the men and women working away at their stations.
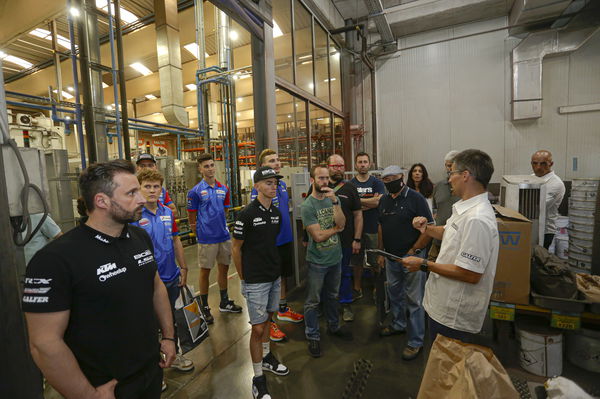
The first stop on the tour is a room that looks like a cross between a Moroccan spice stall and a military arms store. Stacked across the room are strange barrels, brimmed with different compounds that all seem to be varying shades of the colour grey. It’s these compounds and the ratios with which they are mixed together, that give Galfer’s brake discs the stopping power they need. Once the magic mixture is defined, it’s off to be pressed into that familiar shape. Picking a freshly pressed piece of friction material from the line, marketing boss Evo explains how fragile the compound is, crumbling in hands at the lightest touch.
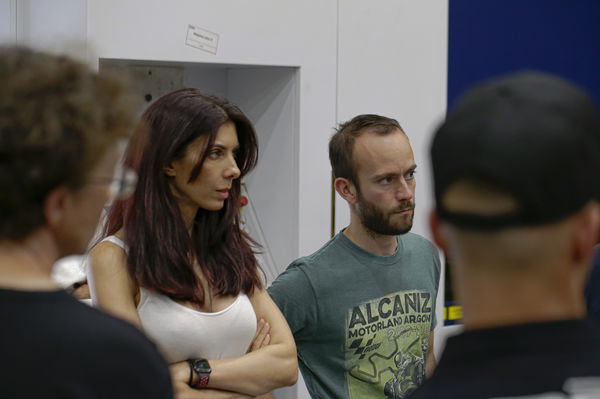
Confused as to how such a fragile material can withstand the rigours of slowing a 200kg bike from 200mph, Evo explains that it isn’t glue that keeps the friction compound together when it’s mated to the baking plate, it is heat. From here the compound is mounted on the backing plate and sent off into small heat-treating stations. These ferociously hot ovens can take around 20 to 30 brake pads at a time and are loaded and unloaded by hand. Once they are baked the elements in the compound bond together, latching on to each other and the backing plate, and fusing the whole lot together as one.
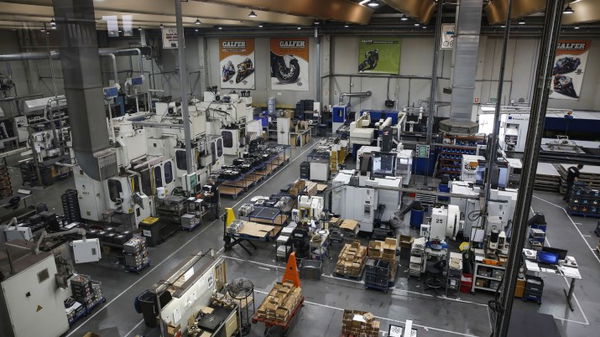
Before any of that can take place though, the mounting plate for the pads needs to be cut, ground into shape, and heat treated. All of that takes place across the factory floor, and it’s a mesmerising process. These million-dollar machines chop through huge steel sheets like a samurai sword through a watermelon – it’s totally mind-boggling. There are a few of these machines dotted about, each doing a different job based on the requirements of the business. From there they hit quality control, where a selection of the pads and brake discs will be checked to ensure they are within tolerance and fit for use.
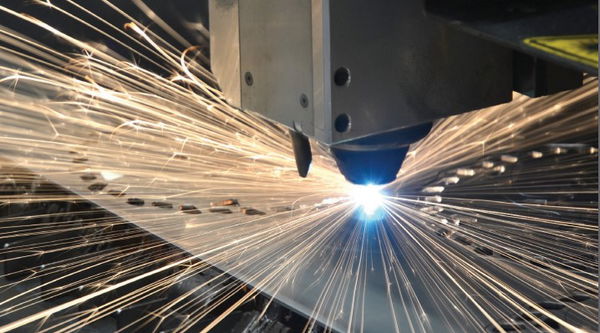
From there we headed into what was probably the most spectacular part of the factory. The Dyno room. Here an operator has a huge machine they can load the discs onto and run it through some seriously rigorous testing. The brake is spun at very high RPM, while a caliper is activated upon the disc to simulate extreme braking events. Spinning at a few thousand RPM we all ‘ohhh’ and ‘ahhh’ like kids at a firework display as the disc glows red hot before cooling once more. They’ll carry out this testing sometimes until the product destroys itself and can even carry out race simulations of specific tracks to ensure the product is up to the task.
From there the pads are processed, packed and shipped, eagerly into the hands of road riders and racers across the world.
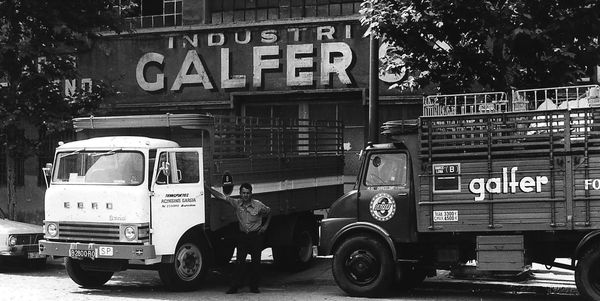
A brief history of Galfer
Like many motorcycle component manufacturers, the story of this manufacturer doesn’t start on two wheels, but on four. Founded in 1952 by Maffio Milesi INDUSTRIAS GALFER S.A. is born, producing drum brake linings and clutches for Seat, and then later some motorcycle makers. It wasn’t until the 1960s that the firm moved into the world of performance brake linings, with its HP6 range of performance linings.
The 1970s saw the brand move away from asbestos in its linings, instead opting for aramid fibre blends. This period also saw the second generation of the Milesi take the reigns of the company.
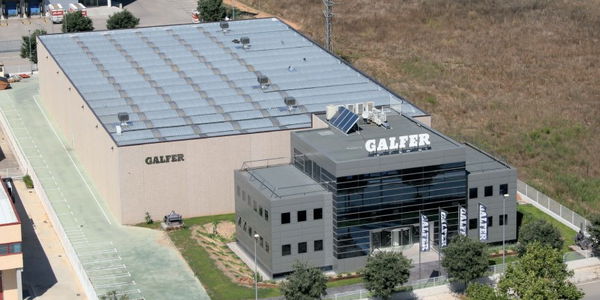
The head office and factory in Spain
We have to fast forward to the 1980s to see the first motorcycle-specific products from the firm, with Ducati being the first in line. Later in the decade, the firm produced its first catalogue for motorcycles specifically, with 45 products and two choices of compounds.
The 1990s was a bit of an important time for the firm, as asbestos use was discontinued, and the USA branch of the firm was established in California. It also saw the company grow significantly, as the production of bicycles and later motorcycles and cars. It also saw Galfer patent its ubiquitous Wave brake discs, a product line the firm still produces to this day.
The 2000s, 10s, and 20s bring us up to the modern day and the company moved to its current home at Granollers just outside Barcelona.
More information on the full range of products can be found here.