BMW WorldSBK team 3D print race parts trackside - 3D printing the way forward?
BMW team make use of 3D printed parts trackside for quick replacements on their S1000RR - is this the next development in motorcycling?
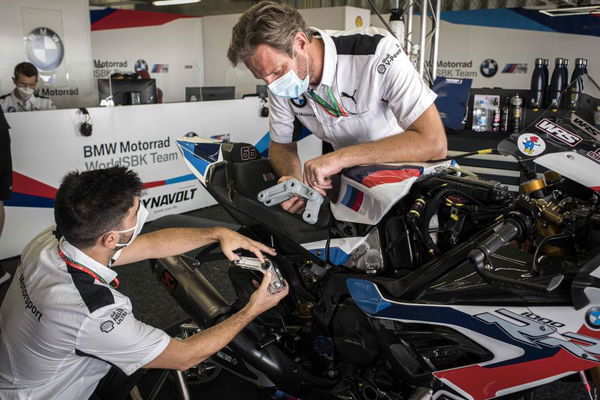
FORGET ink-jets and laser printers, we’re talking about the future here. In the right hands, 3D printers can allow anyone to create anything their heart desires, whether it’s a cup-holder or a precision engineered race-spec part for a superbike.
As seems to be the case, the pioneering tech used by factory teams in the various top race championships (BSB, WorldSBK, and MotoGP bikes) does tend to trickle down to consumer models, giving us a taste of what makes the superbikes of the world really super.
But BMW Motorrad Motorsport in the WorldSBK series, with riders Tom Sykes & Eugene Laverty, has taken a step past trialing new downforce-generating wings and go-faster stripes, and are turning their hands to 3D printing parts for their S1000RR.
WATCH our WorldSBK comparison - including the BMW S1000RR
In the past, they have created a full S1000RR frame from 3D printing tech, and it’s tech that is used on other vehicles from the BMW range, such as their i8 Roadster.
By carrying a portable printer in the team truck, the team is able to skip the typically arduous task of specialist engineers manufacturing a component in a factory for testing, shipping said part to the team, and finally installing it - they are instead able to identify a potential new part, design it at trackside, printing and installing it to check suitability.
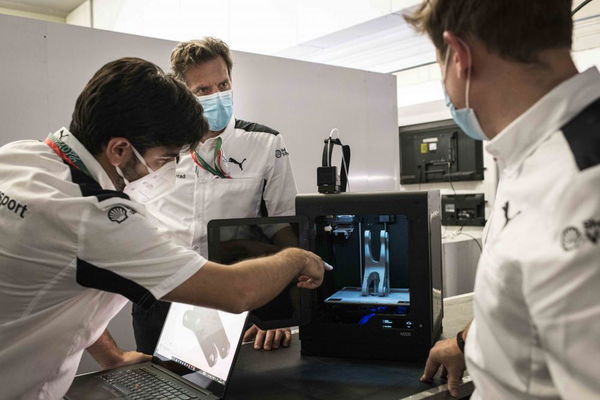
This process will therefore allow Team BMW to optimise and adjust their parts as needed, instantly, by the trackside on a race weekend. If an engineer identifies a potential adjustment to a part that could optimise performance, they can load up the part on CAD and get V2 printed and on the bike. If the new part works as planned, the design can be sent to the factory to be created in a more permanent metal or carbon if needed.
Marc Bongers, director of BMW Motorrad Motorsport, was quoted:
“This technology allows us to make improvements to the RR quickly and efficiently. The developments of a WorldSBK motorcycle is a continuous process and it is often the small details that make a motor better.”
“Behind the scenes, our engineers are constantly working on tuning and optimisation of the individual components of the bike, all within the framework of the changes allowed by the regulations. We can use 3D printing to implement them on the track, even during race events. Then we take the acquired data and subsequent analysis - combined with comments from the riders or input from the mechanics working on the bike itself - and generate input for the development team. This input contributes to the emergence of ideas that can be implemented directly into existing constructions or into simulations and iterative processes leading to new constructions, all performed in CAD.”
“The new components are printed as plastic variants and their functionality and ease of installation are checked directly on the bike. This process is now much faster than when we had to wait for parts to be manufactured in-house or externally and made available for evaluation on the track. It is also easier to gauge potential contact with surrounding parts than on a screen.”
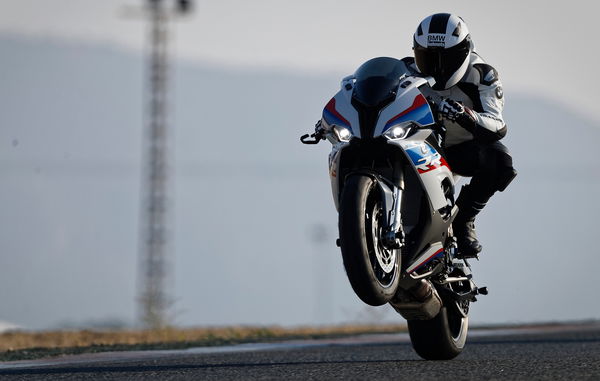
So it’s by no means a fix-all permanent solution, but 3D printing technology allows the team to near-instantly develop a part that would otherwise take much longer, and get the part in the manufacturing queue for permanent install. If it’s a part that would be plastic anyway, or plastic reinforced with carbon fiber, it can be built trackside: such as a quick-release coupling or brake ventilation system.
Where does this leave us, the consumer? One plucky motorcyclist printed a choke lever because the part wasn’t produced anymore, showing that in the face of adversity, ingenuity can prevail. As the technology progresses, there’s no doubt it will become a fantastic option for the industry. In fact, in a recent article, the modular Lacama motorcycle is a result of 3D printing tech allowing for unique parts to be designed. Perhaps not quite the April fools '3D printer in the topbox' that BMW had for us in the past, but not far off.
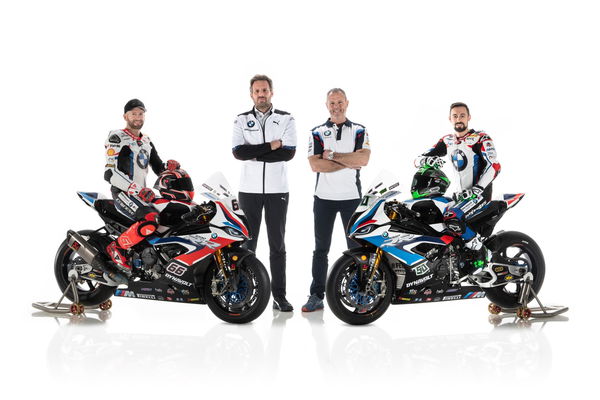
Given the numbers of classic motorcycle and scooters on the roads, with an ever-depleting number of original parts in circulation, we’ll get to a stage where there are no longer original (or perhaps even aftermarket) parts for your garage project, so turning to a 3D printer could be the future option for you fixer-uppers and tinkerers.
Of course, the question has to be asked, can you trust a 3D printed part? Well, if it’s good enough for a WorldSBK team…