How A Motorcycle IMU Works
The IMU (Internal Measurement Unit) is perhaps the most important part of a motorcycle’s electronic package. But how does it work?
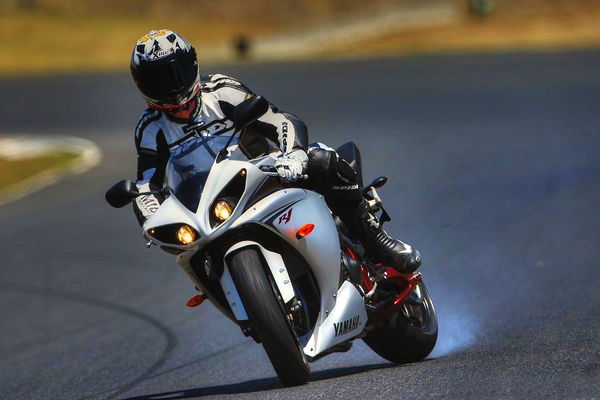
At the turn of the century, traction control was almost half a decade away from entering MotoGP, let alone affordable and accessible road-legal commuter motorcycles. By now, you can have a whole suite of electronic aids, all with adjustable intervention levels and all working all the time, regardless of the bike’s pitch or lean, and for less than £10,000 in some cases. All of that is possible thanks to one box containing a bunch of sensors: the IMU.
Since the end of the 2010s, the new technology has been filtering down from the superbikes that debuted the systems less than a decade before to more mainstream models. By 2019, Ducati’s entire range featured cornering ABS, for instance – even the entry-level models – and within a handful of years we’d expect every single bike on sale, right down to scooters, to be similarly equipped.
Why? Because this potentially lifesaving technology has become relatively cheap, compact and lightweight; it’s almost harder to justify not fitting it. And IMU – Inertial Measurement Units – are the key.
While it’s relatively straightforward to implement either traction control or antilock braking in a straight line – by comparing the front and rear wheel speeds to spot a lock-up or wheelspin, for instance – doing the same thing in corners is much, much harder. As a bike leans over and rolls on to the edge of its tyres, the effective diameters of its front and rear wheels both become smaller, and because they usually have different widths and profiles, they don’t do it in unison. That, in turn, means they will rotate at different speeds, screwing up simple comparative formulas for applying traction control or ABS.
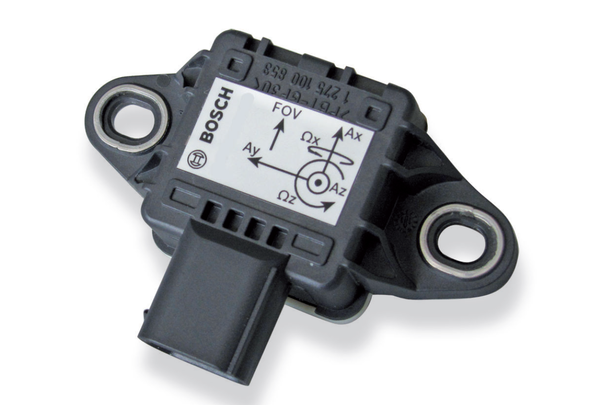
No, to be able to apply the sort of complex traction control or ABS mapping needed to cope with a bike that’s travelling in anything other than a straight line, you need a lot more information. But give the computer knowledge of its lean angle, pitch, acceleration, deceleration and lateral movement – along with the right programming to interpret it all – and the possibilities become endless. Not just lean-sensitive traction control and ABS, but technologies like wheelie control and rear-wheel lift control suddenly become relatively easy to implement, along with all the levels of rider-adaptable adjustment that we’re coming to expect.
The relatively sudden emergence of all this technology comes thanks to two key technologies. One is the adoption of computer-controlled electronic throttles. Now almost universally adopted as a response to Euro4 emissions rules, electronic throttles mean you can give the engine management computer fine control over not only the bike’s fuelling and spark but also the airflow into the engine, allowing it to make the sort of minute and rapid adjustments needed for successful traction control.
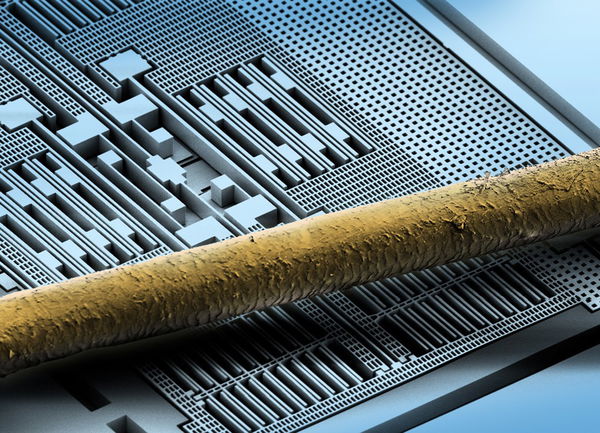
Above is a Bosch MEMS IMU sensor with human hair laying across it
The second technology is that of Microelectronic Mechanical Systems, or MEMS. These are what allow the creation of IMUs.
Although MEMS look much like computer chips, and mount on circuit boards, these are actually tiny mechanical sensors – accelerometers and gyroscopes – that are the key to Inertial Measurement Units.
Accelerometers work using weights suspended on springs, called ‘seismic masses’ – one for each direction (left-right, forwards-backwards and up-down in a three-axis accelerometer). Because the weight is known, as is the rate of the spring, by measuring how far that weight moves away from its static position the sensor can tell how fast the unit is accelerating in a particular direction. This idea isn’t new, but MEMS has made it microscopically small, with comb-shaped seismic masses mounted on silicone springs and sealed in a vacuum along with corresponding fixed-position comb teeth that interlace with those on the seismic mass. As the distances between these pieces change, so does their electrical capacitance, so measuring that reveals any movement of the mass.
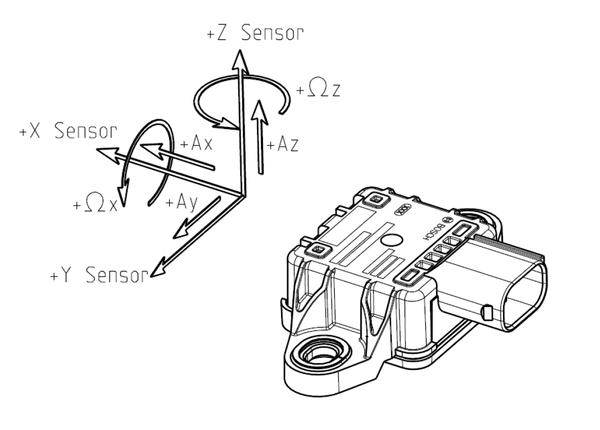
Gyroscopes measure angles of rotation, again in up to three axes; pitch (tilting forwards or backwards), roll (leaning side to side) and yaw (turning in relation to your initial direction). In the earliest of IMUs – like the systems used on Apollo space craft – these gyroscopes were the sort of rotating weights that most of us associate with the word; really not that different from a spinning top.
A modern MEMS IMU has a ‘vibrating structure’ gyroscope rather than those heavy, spinning ones. The idea is that a mass that’s vibrating back and forth will try to keep moving in the same direction even when whatever it’s attached to moves. Just like the seismic masses in the accelerometer, the movement of the gyroscope’s vibrating masses is measured to reveal the corresponding movement of the bike.
All of this happens in a tiny chip that could cost as little as a few pounds. In fact, in mass production, the cost might well be measured in pennies.
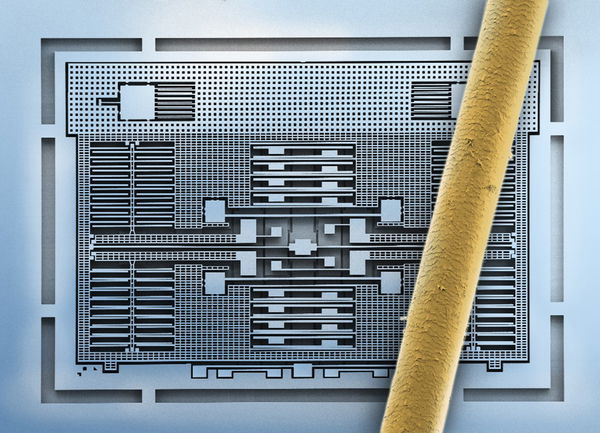
At most on a bike, you’ll get six axes of movement that can be measured – acceleration in three directions and rotation in another three – although many will only use five axes, doing without the yaw measurement of the gyroscope. However, you can actually get MEMS IMU systems that measure nine axes – adding a three-axis magnetometer to the gyroscope and accelerometer sensors. It measures position relative to the earth’s magnetic field; useful in some navigation equipment, but not really a help when it comes to traction control or ABS.
The IMU on motorcycles, whether five-axis or six-axis, hand all their information about the bike’s acceleration and rotation to computers that use it for the ABS and traction control – and, in some cases, for electronic suspension adjustment, too. Allied to other information – throttle position, wheel speeds, brake pressure and maybe suspension potentiometer movement – the computer can build up a complete picture of what the bike is doing and compare its behaviour to pre-programmed maps. So if a measurement starts moving outside a known safe zone, indicating the start of a lock up in the case of ABS or a slide when it comes to traction control, the computer will probably know it long before you do. In fact, it can even start to rein you in before the problem begins – consider ‘rain’ settings, for instance – by putting lower limits on the maximum levels of acceleration it will allow.
It’s all incredibly clever, and it’s technology that simply didn’t exist a few years ago (Bosch, the market leader in the field, introduced its first ever MEMS components in 1998). You may never need to use it, but if traction control or ABS only needs to intervene once in a bike’s lifetime, it will instantly justify its existence.