Compression ratios explained
Fuels rush in, then they get squashed into a tiny space and ignited.
The mysteries of compression ratios investigated and unravelled
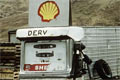
An engine's compression ratio is the ratio of the volume of gas in the cylinder when the piston is at the top of its stroke (top dead centre, or TDC) to the volume of gas when the piston's at the bottom of its stroke (bottom dead centre or BDC). In other words, it's the ratio of compressed to uncompressed gas, or how tightly the incoming fuel/air mix is squeezed into the combustion chamber before it's ignited. The more it's squeezed, the more efficiently it burns and the more power is made.
Apparently small changes to an engine will make a significant difference. 'Skimming' the cylinder head by machining away its bottom face where it mounts flat against the cylinder barrel (which effectively reduces the combustion chamber's volume) or fitting a thinner head gasket will increase the compression ratio, as will fitting 'high compression' pistons with a raised crown. Any modification that reduces the volume of the combustion chamber will raise compression, but it is also affected in other ways too.
Boring out a motor or increasing its stroke gives more power not only by increasing capacity, but also by boosting compression. Say we have a 500cc single-cylinder engine with a bore of 100mm and a stroke of 63.66mm. Let's also say its cylinder has a combustion chamber volume of, for the sake of easy calculation, 50cc. With the piston at BDC, the total volume of the cylinder is 550cc. With the piston at TDC, the volume is reduced to 50cc. Its compression ratio, therefore, is 550 divided by 50, or 11:1. But if we give the engine a 2mm overbore and make no other modifications, its displacement is now 520cc. Total cylinder volume is up to 570cc, reduced once again to 50cc at TDC. Dividing 570 by 50 gives 11.4:1. By increasing the engine's displacement we've changed the ratio of compressed to uncompressed gas volumes, and increased the compression ratio.
Whichever way we go about it boosting the compression ratio is an easy route to more power. High compression pistons are, according to FW Development's Ian Park, "bolt-on horsepower". Modern bike engines tend to run compression ratios in the 10:1 to 12:1 region. By way of an example, a standard CBR600RR has a 12:1 compression ratio, while an FW Developments supersport-tuned RR will run at around 15:1. But there are limits to how high the compression ratio can go. The trouble with petrol is that if it is compressed too much it starts igniting of its own accord, rather than when you want it to. This is known as detonation or 'knocking', and it's this that prevents engines running very high compression ratios.
Compressing a gas raises its temperature, so as the piston rises and the fuel/air mix is compressed, it heats up. In an ideal world the compressed fuel/air mix ignites from a central point in the combustion chamber (where the spark plug is), expanding out evenly in all directions and pushing the piston down (because that's the only bit that can move at this point). Raise the compression ratio too far and a spontaneous auto-ignition occurs towards the outer edges of the combustion chamber, instigated by the sudden rise in cylinder pressure when the spark plug ignites, instead of burning outwards from a central point.
This uneven, spontaneous burn produces amplified pressure waves in the combustion chamber. A metallic knocking sound can even be heard from the engine as these high pressure waves hit the piston crown and the sides of the combustion chamber, hence the term 'knocking'. While these pressure waves are very short-lived, they are higher than normal combustion pressure - and temperature - and can cause all sorts of problems, from blown head gaskets to damaged pistons and overstressed rods and bearings. Overheating can also be a problem.
A fuel's octane rating is a measure of its resistance to detonation - the higher the rating the more it can be compressed without detonation occurring. Normal unleaded pump fuel with a 95-Ron octane rating is fine for most standard engines' compression ratios, but even mildly-tuned engines might need 97/98-Ron super unleaded fuel to run safely.
STATIC V DYNAMIC COMPRESSION RATIOS
Things are never as simple as they first appear. The compression ratio quoted in technical specification panels is only part of the story. That compression ratio figure is actually what is referred to as 'static compression'. The static compression ratio isn't necessarily achieved by a running engine.
Static compression is simply a calculation comparing two volumes: the volume of the combustion chamber, and the volume of the combustion chamber and cylinder with the piston at BDC combined. We need to look at 'dynamic compression'.
The four-stroke cycle works like this: the piston descends as the camshaft opens the inlet valve, sucking fuel and air in. When the piston reaches BDC, the inlet valve closes and the piston begins to rise, compressing the fuel/air in the cylinder until the piston reaches TDC. The spark plug then ignites the fuel/air, forcing the piston down to BDC. As the piston starts to rise again, the exhaust valve opens and the burnt gas is expelled. The cycle starts again. However, if an engine is to work efficiently at high rpm - as modern performance engines do - they have to run relatively extreme camshaft timing. There are two factors to consider with cam timing: 'lift' and 'duration'. Think of the valve as a door into the cylinder allowing fuel in. Lift is how far the door is opened, duration is how long it's open for. At high rpm, an engine needs to get gas in and out very, very quickly indeed. So quickly that relatively extreme cam timing is needed to get enough fuel into the cylinder to work at high speed. With 'normal' cam duration, an engine won't be able to run at very high rpm simply because the inlet valve isn't open for long enough to get sufficient fuel into the cylinder in the time allowed.
You'd be excused for assuming that once the piston reaches BDC on the induction stroke that the inlet valve would be about closed, and that as soon as the piston began ascending on the compression stroke, the valve would be firmly shut. On low-revving, low power engines this may be the case, but on higher-revving engines the inlet valve actually remains open some way into the compression stroke.
The problem with this is that the piston is rising as fuel/air is still trying to enter through the open inlet valve, which means the gas already in the cylinder can't be properly compressed. At least not at low rpm, when the gas still flowing in is travelling relatively slowly. As the piston ascends, the gas in the cylinder is compressed upwards towards the still-open inlet valve. But it can't be properly compressed and it tries to escape back out via the inlet valve, interfering with the incoming fuel/air. The static compression ratio can't be achieved in a high-revving engine with a long duration inlet cam.
However, at high rpm the incoming fuel/air mix attains such a velocity that it is able to rush into the cylinder unhindered despite the ascending piston forcing gas already in the cylinder upwards, and maximum possible compression is attained.
This is why high-revving, high-performance engines are unable to perform as well at low rpm - their relatively extreme cam timing won't allow sufficient gas flow into the cylinder or effective compression of it once it's there.
The effective drop in compression caused by the long-duration cam timing of high-revving engines is one of the reasons race-tuned motors need to run higher compression ratios than standard, as FW Development's Ian Park explains: "Every time you increase the cam duration you're dropping the compression ratio. A lot of that extra compression is to replace what the cams take away. A supersport engine with 15:1 static compression may only be running at 7 or 8:1 dynamically."