The story of Akrapovic
From a shed in Slovenia, Igor Akrapovic's exhausts now dominate the world
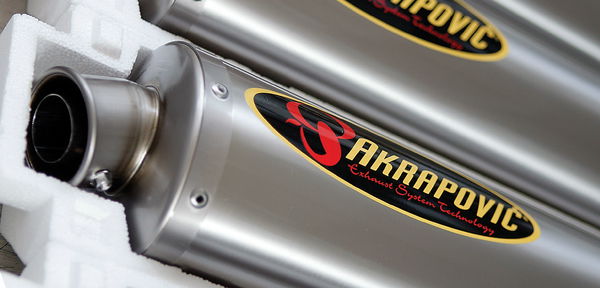
![]()
In just 15 years Akrapovic has come from a one-man-band making exhausts in a shed to being the number one brand worldwide for road-riders and race teams alike. Stories like this generally start with a visionary, and this is no different. Ours is Igor Akrapovic. Igor was working in his father's factory making injection-moulded plastic goods, while in his spare time he was making engines and tuning stuff for his friends, as well as indulging in a spot of racing. This was the late 1980s. And while doing all this work for himself and his friends, Igor pretty soon realised that everything was available for racers except good quality exhaust systems offering big performance advantages. From his hobby has spawned his company."Really, I'm just lucky to have made a hobby that I loved so much into a job," admits Igor. "This part of the job, working with the engines, I love and find most enjoyable." Thankfully, Igor has managed to bring together a team of people (176 at the last count) to allow him to do what he does best. Tinker with engines and develop exhausts for them. Officially setting up in 1990, Igor was joined in 1992 by Slavko Trstenjak (pronounce his name Slough-co!), an electrician with a similar aptitude for tinkering and tuning, while Marko Adamic joined as sales manager a year later. Marko says: "We started out as a small team. Igor, Slavko and me. As the business grew we were together all the time. Even as we were growing in size the morale has been very good. People want to work for us. Our rates of pay are up to 100% more than Slovenia's average wage. That's Igor's policy. He wants the workforce to really want to work here. Most of the employees are interested in racing. The results are printed after every racing weekend and posted up on the walls. They want to know if the bikes with our exhaust systems have won." Igor adds: "This is a big part of what makes us successful. The workers have to have a passion for what they're doing, they have to have a passion for motorcycles. That way they give 110%."At the start Igor spent half his time tuning engines and the rest building exhausts. His first products were well enough received that soon the decision was made to concentrate solely on manufacturing exhausts. The small 'workshop' was in fact a house, and pretty soon things would get too big for its 450 square metres. The house is still there, a good stone's throw from the 7000 square-meter modern factory that Akrapovic has resided in since 1997. Things really picked up in the early 1990s, thanks to Igor's intuitive knowledge of engines and a range of then-new techniques and materials."I started out as Igor's helper," remembers Slavko, "Igor would do pretty much everything himself. He would strip and re-build motors, change valve seats, the lot. He'd even test the bikes. The only thing he didn't do was the welding. " Igor and Slavko began to use new configurations of tube diameters, crossover tubes and conical headers as well as using thin-gauge stainless steel, titanium and carbon-fibre. Shrewdly, Igor invited Kawasaki Deutschland to test his new exhaust. The team found it was better than the factory system, and it was the beginning of a remarkable roll. From a number of German Pro-Superbike teams, Akrapovic grew to dominate in superbike racing across the globe, with every single Japanese manufacturer using Akrapovic exhaust systems during the 1999 World Superbike season!"And our badges meant our exhausts on the bikes," explains Igor. Just because it said one thing on the exhaust didn't mean it came from that manufacturer. For many years it was often a factory exhaust with an aftermarket supplier's name emblazoned on it, for which they'd pay handsomely. Rossi's Honda V5 of a couple of years back? Akrapovic exhaust, that. So why didn't it have the Akrapovic logo on it? Money and sponsorship. Valentino and the Repsol team had a sponsorship deal with Polini exhausts so, instead of the accolades, Akrapovic were paid by HRC to be a silent partner and do some development work. One of Rossi's original RC211Vs is still at the Akrapovic factory today. The funniest thing of all is that Polini only make scooter exhausts. Either way, it's something that Akrapovic can't be drawn on, as they have a good relationship with the Japanese manufacturers. Even though... "they once told us they had made a copy of one of our exhausts," says Marko. "They wanted to see if they could do better. Their exhaust made two bhp less than ours!" If there's a comparison to be made to others in the business it's with Yoshimura. Legendary tuner Pops and his son Fujio made a range of top products. Similarly to Akrapovic, their exhausts work well because they're engine tuners, and the quality of their workmanship is second to none. Like Yoshimura, Igor eventually put his name to his products. His exhausts were originally called Skorpion for the first seven years of trading, before friction with other holders of that name (albeit with a different spelling) in the car exhaust world led to a name change. And what better than the name of the man himself? And if you want to know how to pronounce it, say 'A-KRAP-o-vich'. Okay? And since the successful name change they haven't looked back. Although some might say their exhausts are plenty pricey to your average punter. "The extensive use of crossovers does make a big difference to performance, but also to the price," smiles Slavko, in reference to Akrapovic's trademark convoluted, tapered pipework. "Top performance is always a little more expensive.",br> And the continual search for performance year-on-year will always come at a price. "We're trying really hard to make improvements to our products every year," explains Igor. "As engines get better we have to work with these new engines and make exhausts that improve with them. It's continual." After doing so much to pioneer the use of exotic materials, a new one is now being used. Inconel is twice the price of titanium but, while titanium can get as brittle as glass with constant stresses and heating, Inconel is much more durable - and all for the same weight as titanium. Currently the material has only been used in Akrapovic's work for F1 teams and the doomed Aprilia RSV Cube MotoGP machine. So is it this bold, pioneering use of new ideas and materials that has made Akrapovic what it is today?"Why is Igor so successful?" Asks Slavko. "It's because he has very big balls and he makes the big decisions. Buying that first tube bending machine was a big gamble and a huge investment. Switching from the old, small factory to this one was another big investment. He knows it's all down to him." The final words must come from the man himself. Igor, what makes your exhausts the best? "We know how engines work," he shrugs. "We've been tuners, we've worked on engines and that means we can make the exhausts work for those engines. After that we put in so much effort. We explore different ideas and do a minimum of 200 dyno runs to get something that works. We also have extremely high quality control, and try to use the best possible people." And finally, what of the future? Can Akrapovic continue to grow?"We hope so," he says. "Sure, we see the sportsbike market shrinking a little, but we are diversifying into the motocross and enduro market with partners such as KTM, and are also moving into the All-Terrain Vehicle market which is huge in the USA. We also like to keep ourselves busy with small projects such as work with ultra-light aircraft, bicycles, anything really." WHERE THE HELL IS AKRAPOVIC? Geography and history lesson here. Slovenia was part of the former Yugoslavia. It's capital is Ljubljana (say Loo-bee-yana) and the Akrapovic factory is an hour from here. Slovenia is bordered by Italy in the west, Croatia and Hungary in the south and west respectively, and Austria in the north. Much of the conflict and troubles that affected neighbouring Croatia has not affected Slovenia, although the country did achieve its independence in a 10-day war in 1991. It's a beautiful place to visit, with its own stretch of coastline on the Adriatic, so why not ride there for the independence celebrations on 25 June. And yes, the chicks are hot FAST FACTS First exhaust built in 1990. In '94 2500 were made, and 5000 a year later. Last year 38,000 units were sold The factory used 100 tons of titanium in 2004, with 90% of it coming from Japan. Most of their stainless steel and aluminium comes from Italy Best selling exhaust? Anything for an R1, although GSX-R1000 systems are catching up Exhausts with the most variations? Either the Kawasaki ZX-7RR or Honda's SP-1/SP-2 |
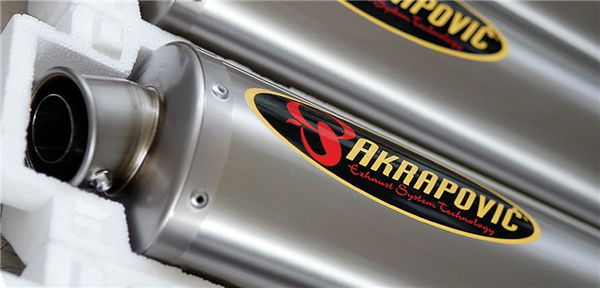
In just 15 years Akrapovic has come from a one-man-band making exhausts in a shed to being the number one brand worldwide for road-riders and race teams alike.
Stories like this generally start with a visionary, and this is no different. Ours is Igor Akrapovic.
Igor was working in his father's factory making injection-moulded plastic goods, while in his spare time he was making engines and tuning stuff for his friends, as well as indulging in a spot of racing.
This was the late 1980s. And while doing all this work for himself and his friends, Igor pretty soon realised that everything was available for racers except good quality exhaust systems offering big performance advantages. From his hobby has spawned his company.
"Really, I'm just lucky to have made a hobby that I loved so much into a job," admits Igor. "This part of the job, working with the engines, I love and find most enjoyable."
Thankfully, Igor has managed to bring together a team of people to allow him to do what he does best. Tinker with engines and develop exhausts for them.
Officially setting up in 1990, Igor was joined in 1992 by Slavko Trstenjak (pronounce his name Slough-co!), an electrician with a similar aptitude for tinkering and tuning, while Marko Adamic joined as sales manager a year later.
Marko says: "We started out as a small team. Igor, Slavko and me. As the business grew we were together all the time. Even as we were growing in size the morale has been very good. People want to work for us.
Our rates of pay are up to 100% more than Slovenia's average wage. That's Igor's policy. He wants the workforce to really want to work here. Most of the employees are interested in racing. The results are printed after every racing weekend and posted up on the walls. They want to know if the bikes with our exhaust systems have won."
Igor adds: "This is a big part of what makes us successful. The workers have to have a passion for what they're doing, they have to have a passion for motorcycles. That way they give 110%."
At the start Igor spent half his time tuning engines and the rest building exhausts. His first products were well enough received that soon the decision was made to concentrate solely on manufacturing exhausts.