Looking through the window - a tour of the MV Agusta factory
A guide through the wonders of how the stunning MV Agustas are born
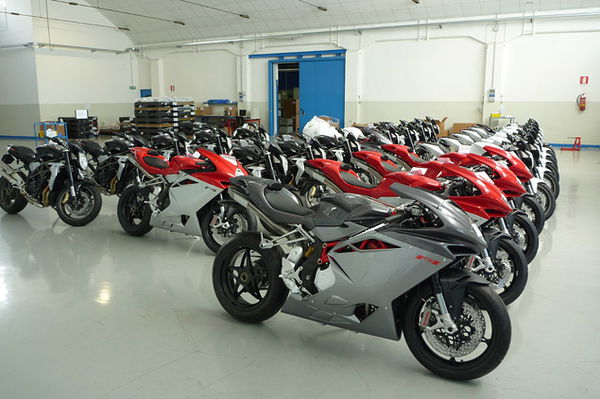
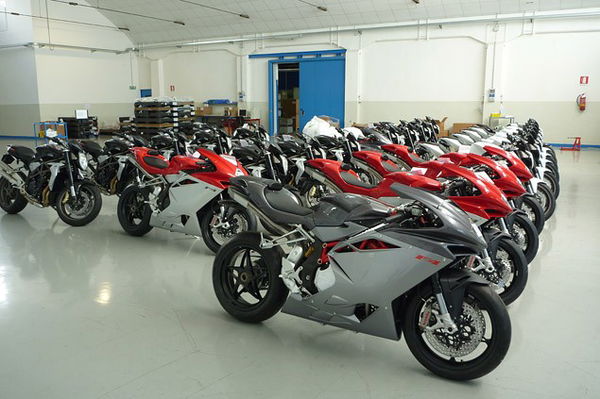
It starts with a pencil. A pencil like any other, that writes and draws. Well not quite like any other, as these words come from an MV Agusta pencil.
The lead feels precise like a 2H, not smudgy and dull like an HB, nor too scratchy and brittle. Surrounding the lead is black wood, with a matt black coating. Towards the top there is a silver MV Agusta logo, that gives the impression of being embossed. To crown everything, a 14 sided obsidian jewel capping the end.
This sums up MV's approach to motorcycle building. Nothing is done by halves and there is no sense of 'oh that will do'. With bike prices coming under close scrutiny in recent times, a trip to the MV Agusta factory was in order to see exactly what you get for your money. (Which nowadays is only a smidge more than offerings from the land of the rising sun).
Perched on the banks of Lago di Varese, 30 minutes from the Italian-Swiss border and moments from the best roads and alpine passes ever constructed, the MV factory boasts one of the worlds most idyllic locations for any manufacturer. Arrive at lunchtime and you will see employees fishing by the lake shores, jogging a lap of the adjacent parkland or indulging in a refreshing gelato.
It is obvious when its time for work to commence again as there is a ten to two thunder rumbling in the distance, as enthusiastic fabricators, welders, painters, engineers and designers race back from their lunch break on bikes. A generous 'family' discount ensures many of these are from the MV Agusta and Cagiva range.
Once inside the hallowed gates, it hits you. The history, the achievement, 75 World titles and 270 Grand Prix victories; Agostini, Surtees, Hailwood and Read all had their championship winning bikes built here.
The tour started in Signor Castiglioni's office, which isnt the norm, but it gave an insight into the passion that has fuelled this family to build the Cagiva brand from the remnants of Aermacchi AMF, save Ducati from closure, and since 1992 inject life and dynamism into MV Agusta.
First stop is the engine department, where the heart and soul is crafted. Full design and assembly takes place in house, with cylinder heads and blocks arriving in rough form awaiting a session in the CNC milling machine. Once each port has been flowed and valve seat cut, the finished parts are sent a whole 3 metres away to a test room where a rather serious looking man with a good Italian name and trendy spectacles is in charge of the only robot at the factory. This so called robot uses lasers to check that the very tightest of tolerances have been achieved. Once he is happy and the computer says yes, another team take over, inserting the valves, springs and camshafts all by hand, using proper hand tools.