BMW's latest carbon-fibre technology for bikes
Munich firm's Motorrad division shows us the details behind its future carbon tech
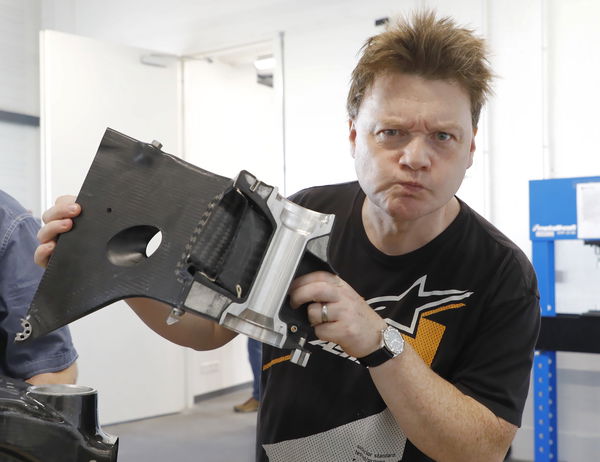
WE WERE at BMW’s super-secret R&D centre in Marseille at the weekend, where we saw some of the firm’s latest work - like its autonomous bike research. And one of the most interesting areas covered by the engineers was its developments in carbon-fibre.
At one end was, of course, the very high-end production of the frame, swingarm and wheels from the HP4 Race. The engineer in charge of the presentation, Michael Heimrath, took us through the ins and outs of the production and testing processes, and how BMW can guarantee that the frame will stay safe for use over the long term (ten years-plus). Stresses, environmental effects, abuse – it all has to be taken into account.
The first part we looked at was the frame – and BMW had a halved steering head on show. There are several tricky issues here: getting the stiffness right in the correct directions, putting in metal (aluminium) fixings to take bolts, and bearings and the like, and dealing with thermal expansions.
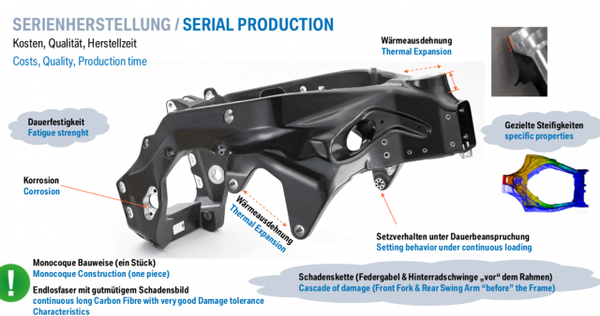
Stiffness is a big part of making a chassis ‘feel’ right to a rider. Make a frame too stiff in the wrong areas, and you get reduced feedback, poor suspension performance, and a nasty performing chassis overall. BMW’s worked hard to keep the carbon frame super-stiff in the correct areas – keeping the wheels in line for example – while allowing some flex.
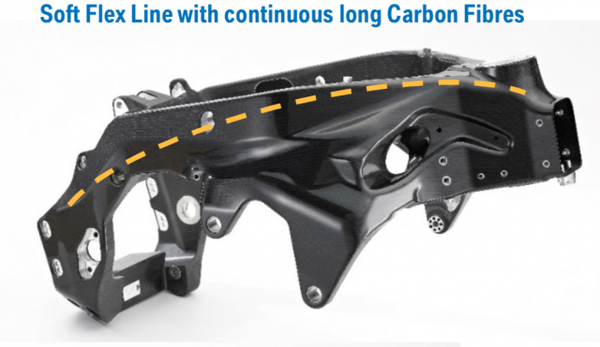
That’s been done by adding extra carbon-fibre weave in certain areas, and by using directional carbon-fibre material tapes. The hollow parts are mostly filled with lightweight foam (to keep water out – trapped water can cause long term damage), while some hollow areas are left empty, to act as a progressive crush zone in a bad crash.
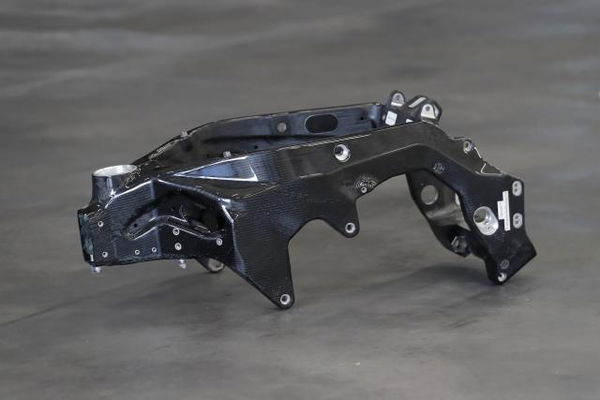
Fitting bolts and fasteners to carbon is a big problem. You can’t just bolt parts like the engine straight into the carbon – you need metal inserts. These need to be glued into place, and also specially treated to stop 'galvanic' electrochemical reactions between the carbon and aluminium. The same applies to bearing seats, like the steering head.
This leads to the last problem we looked at – thermal expansion. The alloy parts expand and contract much more than the carbon-fibre. Over years, this can cause cracking or failure. So BMW attaches the aluminium parts in such a way that they’re ‘pre-stressed’ - like steel bars in concrete. So the carbon-fibre holds the aluminium part in a stressed state, so as it expands and contracts, there’s no movement between the two.
Lastly, the engineers need to consider thermal movement in the engine mounts too. The whole engine obviously heats up when running, and the two side mount bolts change their position by up to 2mm. So if the super-stiff mounts weren’t designed to accommodate this, there would be huge stresses created every time the engine heated up and cooled down.
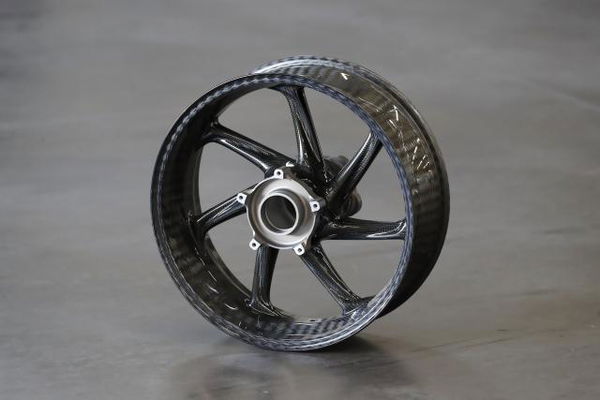
Apart from the frame, the wheels took most attention in terms of testing. They are obvously super-critical in terms of safety, so BMW has gone properly belt-and-braces for its test procedures. The wheels – which are made in-house by BMW, not by BST or another third party supplier – go through testing hell to make sure they’re as safe as aluminium wheels.
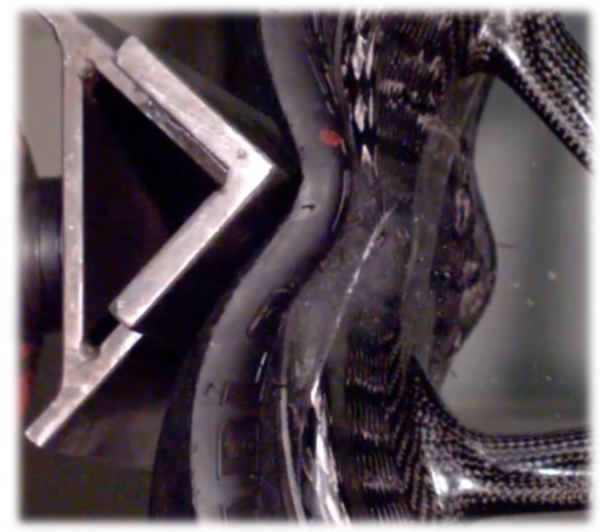
Firstly, BMW calibrated its test rig with an aluminium wheel, to see what forces were involved. Then it used these force levels on the carbon rims. A 90-degree angle-form anvil is smashed into the wheel rim, to simulate hitting a kerb, or an obstacle in the road at speed. The BMW rims are designed to fail-safe: they stay in one piece, and slowly deflate the tyre, so the rider knows the wheel is damaged, but can come to a halt safely.
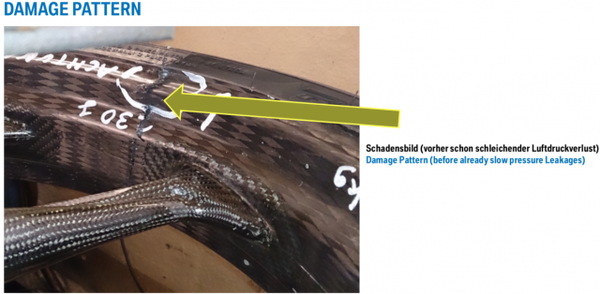
The testing department went through the official German TÜV testing for government approval of the carbon wheels. But they then repeated the tests, after damaging the wheel with the kerb-angle kill test. The wheels still passed all the TÜV tests, even with the rim damage from the high-speed kerb impact destruction simulation. Test engineers even put the bike wheels through the extra punishment of a car wheel test – checking for side impact absorption and bending circulating tests, and again they passed.
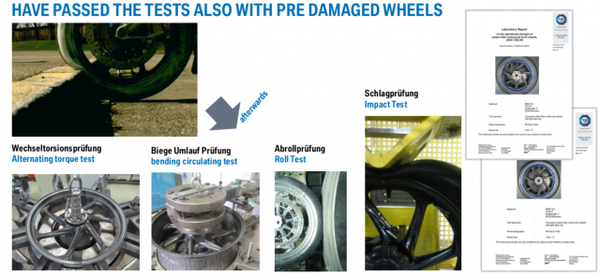
The wheels and frame and swingarm are also tested for resistance to landing shit wheelies (just as well for some of us…), and also tested after environmental stresses – they get heated up and cooled down, soaked in water, rubbed with harsh salt, and generally abused. Wheels go through thousands of hard braking cycles to check how they cope with the heat through the disc mounts. Engineers even drop a whole bike onto a concrete block, simulating a bike falling off its stand onto a kerb, and giving the frame rails a proper bashing, to see if the test results hold up. Impressive stuff.
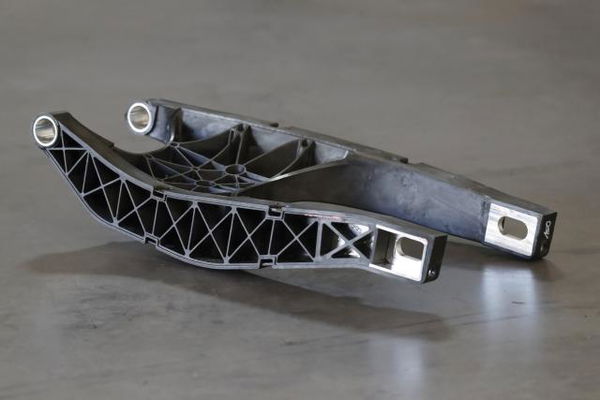
The last thing BMW showed us was pretty cunning – and applicable to far less fancy bikes than the £65k HP4 Race. The engineers had a carbon swingarm (above), which can be made in three different forms, using the same injection moulding tool. The most basic form is suitable for a 30-50bhp power output, with carbon-reinforced plastic construction - the internal ribbing you can see there makes it super-stiff for its weight. The next version has some carbon-fibre inserts placed inside the same tool before the carbon-reinforced plastic is injected in. That then forms around the stronger carbon-fibre inserts – making a slightly pricier swingarm, that's much stiffer and can deal with 100+bhp power outputs.

Finally, the engineers showed another version (above), with outer carbon-fibre plates as well as the inserts moulded into the unit, which can cope with more than 200bhp. So, the same expensive mould can be used to make a wide range of swingarms, cutting costs (the basic swingarm could cost just €30 to produce, apparently) and improving flexibility for production engineers.
Expect carbon to work its way down the bike food chain then - innovations like this swingarm design show that BMW isn't just tied to using the fancy fibres on its megabucks machines. Lower-priced carbon chassis parts designed for more working-class bikes? Sounds great to us.