Automatic: How Honda's future will affect you
A look at the technical side of Honda's new Integra. You might not want an automatic gearbox, but Honda's future-tech innovations could influence the next bike you buy
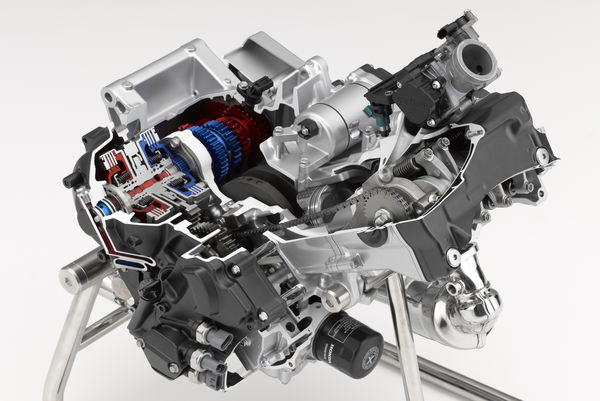
Honda has put a significant chunk of investment into gearbox automation over the years but they've ramped it up recently with Dual Clutch Technology (DCT), as seen on the VFR1200FA and now DCT is in its second generation in the new Integra.
Clearly Honda believe it's the future, you might well disagree. Honda's research sample spent more than 80% of their time under 6,000rpm and 90% of their time under 90mph. This new engine and its technology is the answer to that research.
However, in creating the new engine for the 'don't call it a scooter' Integra you can see above, Honda have developed some really interesting technology that could help make their other - let's call them traditional - motorcycles, lighter, faster and more fuel efficient.
Honda's target for this new engine was to make it 50% more fuel effiecient than engines in the same displacement class whilst also making it user-firendly and easy to package.
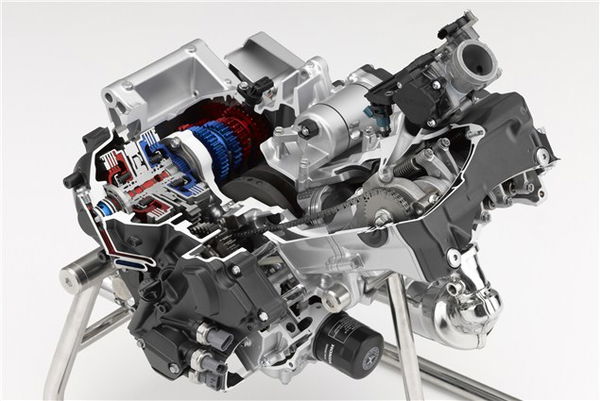
Here it is, the new engine that powers the Honda Integra (and will power at least two - more convential looking - new models due to be revealed within a few days).
It's a 670cc, liquid-cooled parallel-twin, with a forward-leaning angle of 62°. It uses a 270° crank (as made famous on the TRX850 but an invention patented by Honda in 1985). It also runs Honda's second-generation DCT gearbox. The stroke is longer than the bore is wide (undersquare) which, today, is pretty unusual unles you're Royal Enfield.
So on first glance, not much new and revolutionary here you might think.
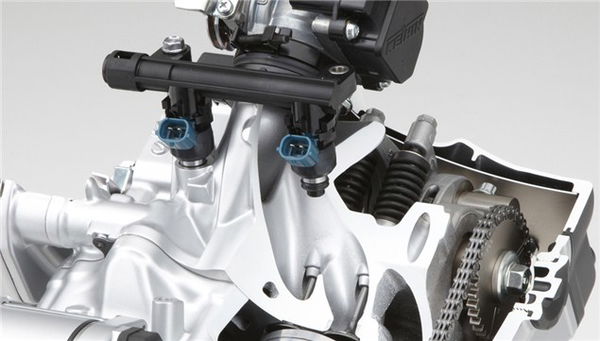
But the whole engine is bristling with space and friction saving tricks. First up in Honda's quest to make the most from the least is its single intake port. The air intake branch manifold has one inlet for the throttle body and this feeds both inlet ports. Honda have gone to great pains to ensure that the aluminium casting's volume is extremely accurate which involved complicated cooling anaysis calculations.
The downside to this is that airflow is not as controlled and smooth as it would be with a conventional setup. The pulses from one port will always affect the other. However, Honda have factored this into the engine's design and coupled with the 270° crank, this small airflow disturbance helps to generate subtle combustion variations, which results in more of the thing we like: character.
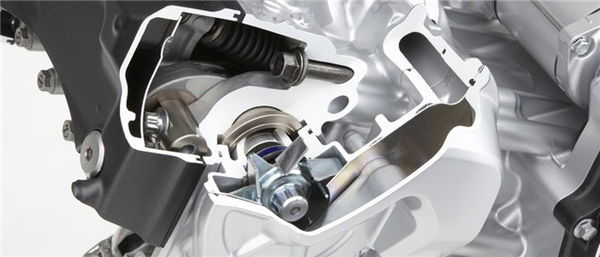
Unconventionally, the water pump is located on the left-hand side of the cylinder head in the upper part of the engine. It's driven off the end of the camshaft, so there's no need for another energy-sapping shaft and the total engine size can be further reduced.
Added to that, the whole cooling system can be made smaller and lighter too; the hosing used to pipe water around is one-third shorter than that of a conventional engine. Less piping means less volume of water too, so there's an additonal weight saving right there. Warm up time is reduced, too, thus improving both CO2 emissions and fuel efficiency.
Honda recognised that with a 270° crank, the vibrations could be eliminated using a biaxial balancer (two balancers). However, the point of the 270° crank is to give the engine character, so two balancers would be working against this. Therefore, only one balancer is needed, thereby saving weight and space. The contra-rotating balancer is gear driven off the crank.
The crankshaft itself uses a pioneering technique borrowed from Honda's automotive division to cut down on waste material and machining time. In essence, a conventional 360 degree crank is twisted through 90 degrees whilst still hot and malleable to create the desired crank pin offset.
The oil-pump is run off the balancer-shaft, which in itself isn't a revelation but - yet again - reducing the number of shafts required means the engine saves weight and increases efficiency. An accumulation of points makes prizes, as they say.
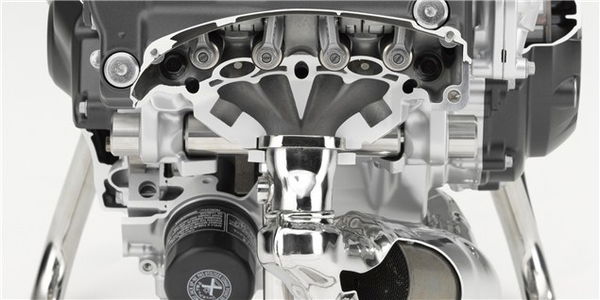
When it comes to the exhaust, there are a couple of clever things going on. Firstly, the exhaust ports have been brought together inside the cylinder head, meaning there's only one 'downpipe' required.
The second is a result of the first: now the catalytic converter (only a small one needed) can sit much closer to the engine. The advantage of this is that a catalytic converter works more efficiently when it's hot. The gases pass straight into the cat, meaning it heats up faster and therefore reaches optimal efficiency more quickly. The more efficient cat can now be smaller, helping to decrease the engine's overall size.
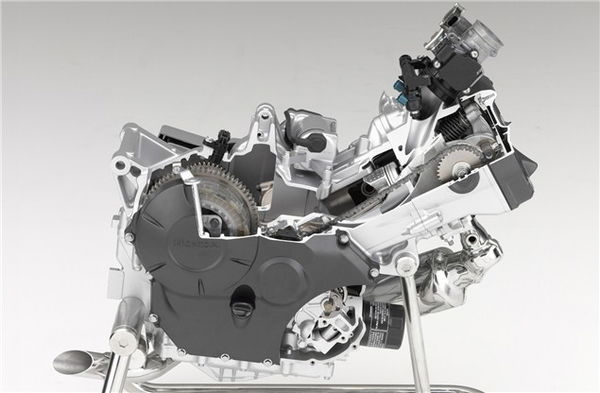
For the valve gear, Honda have used an aluminium rocker arm (as opposed to the more usual steel) to save weight and reduce losses. The pistons have also been treated with an undisclosed friction reducing coating to increase their efficiency and again reduce losses to the overall output.
The result of this is an engine that matches a CBF600 in terms of roll-on times, but at the same time, it's over 50% more efficient. The increased efficiency means the fuel tank can be smaller for a given range, again, aiding weight reduction.
The Integra's twin-clutch constant mesh gearbox is a development of the system first seen in the VFR1200FA. The use of this transmission system fulfills the design brief that the Integra has to be easy to ride to attract not only those who want to ride a motorcycle but those that 'need' to as a transport solution. Details are sketchy here, but from what we can make out on the basic drawings, the gearbox and crankshaft run in a semi-dry sump to avoid the frictional losses of thrashing around in a bath of sticky oil.
We give Honda a big (yet efficient) pat on the back for taking such a fresh approach...