10 fascinating facts about the BMW Motorrad factory
We took a tour of BMW Motorrad's sprawling Berlin factory, and learned plenty along the way
When BMW unveiled its all-new R1300 GS recently, the location it chose to do so was its historic ‘Motorrad’ factory in Berlin. BMW also used the occasion to open its new factory visitor attraction, ‘BMW Motorrad Welt (world)’ and also give the world’s press a tour of the whole manufacturing facility.
We, meanwhile, took the opportunity to dig out some nuggets of knowledge, factoids and more about the place, which you might never have known before…
It all started in 1969. Sort of…
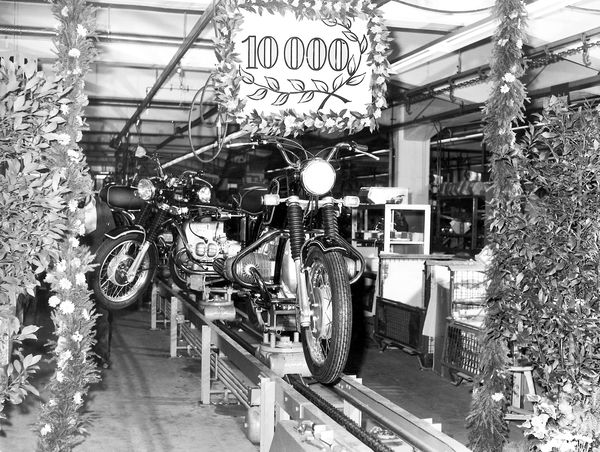
The bulk of BMW’s motorcycle production has taken place at its factory in Spandau, Berlin, since 1969 when it commenced manufacture of the new 5-series after moving production from Munich to free up its car facility. The Spandau factory itself, however, dates much further back. A former Siemens aircraft engine plant, it was taken over by BMW in 1939 and during WWII produced aero engines for the likes of Junkers.
After the war, with aero production prohibited, it was rebuilt and began making, first, tools for BMW’s Munich plant, then from 1949, components for BMW’s motorcycle plant in Munich. Car components were added in 1958. Its buildings, some dating back to 1830, are among the oldest in the whole BMW group.
All BMW’s bikes are built there. Nearly…

Of BMW Motorrad’s current 34-model line-up, 29 of them are built at Berlin-Spandau. The only ones that aren’t are the two CE-04 and CE-02 electric scooters and the two A2-licence models, the G310R and G310GS, which are made in India by BMW’s partner, TVS (although the CE-04’s motor and battery ARE made in Berlin). Spandau also still makes some components for BMW cars, most notably brake discs.
You can visit, too
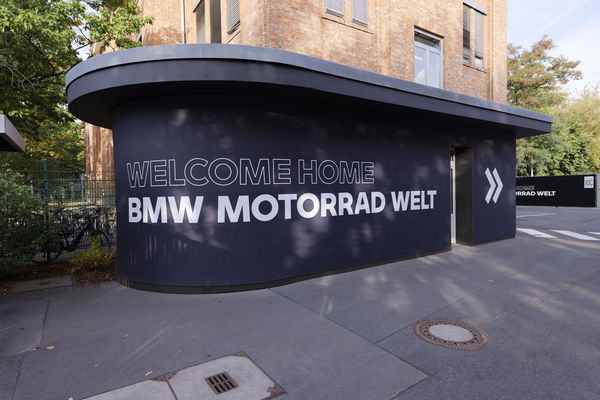
Factory tours of the Berlin BMW Motorrad plant have been available for years (although interrupted by COVID-19), along with those of other BMW plants in Leipzig and even Oxford (MINI). With the opening of BMW Motorrad Welt at Spandau (BMW’s new visitor centre) it’s now expecting even more visitors.
“We normally have 20,000 visitors a year,” says Helmut Schramm, Head of BMW Plant, Berlin. “But with BMW Motorrad Welt we are hoping for much, much more. We are creating a full-size brand experience that connects BMW with its customers.”
It's the biggest in the world. Sort of
Over two million BMWs have been built at Spandau since 1969. With over a million of those being the GS model alone, as first launched in 1980. In addition, with sales last year of over 200,000, BMW now claims to be number one in the world ‘premium’ motorcycle class. Uniquely, all its bikes are now built to order. Around 900 bikes are made a day, or one every 2.3 minutes, with 80 per cent going for export. The whole plant covers 230,000 square metres and employs around 4,000 people.
It's already been making R1300GSs for months
When we visited in late September, new R1300GSs were already rolling off the assembly line, mostly both for the imminent press launch and for distributor press fleets around the world. The company invested over €250m in the plant for the new R1300GS engine and to update old machinery.
It all starts at the milling plant
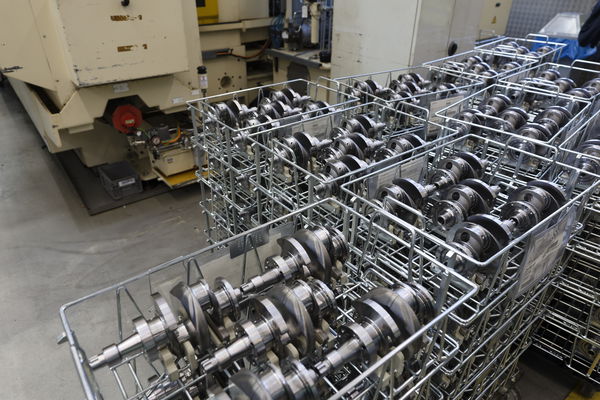
Motorcycle production starts, effectively, in the factory’s milling plant, where 100-plus CNC milling machines in turn ‘machine’ raw engine castings such as cranks, conrods, pistons and heads which arrive from outside suppliers. With the crankcases alone, roughly 2kg of material is machined off the rough forgings, with the ‘waste’ all being recycled.
The factory has a ’Central Nervous System’
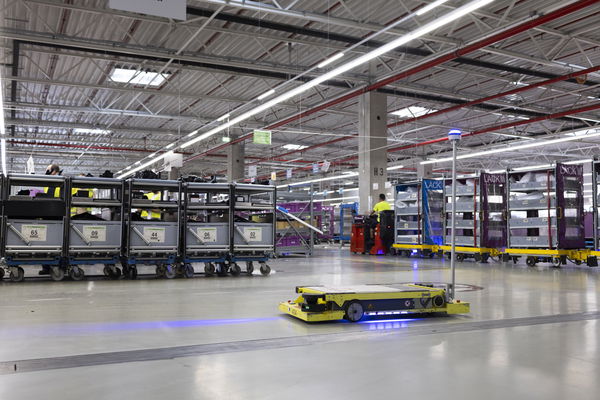
That’s how BMW staff refer to the plant’s huge Logistics Centre, the central hub for the arrival, storage and distribution of all the components required for assembly. It alone covers 30,000 square metres over two floors; 100 trucks arrive per day carrying quantities of the 13,000 components supplied by external suppliers (the remaining 4000 are made in-house); the movement of parts is highly automated via computerised conveyor belts and robot vehicles and most of the parts are sequenced or organised into ‘Bike sets’ to aid assembly. BMW claim it’s probably the most sophisticated logistics set up in motorcycle manufacturing anywhere in the world.
Robots are everywhere
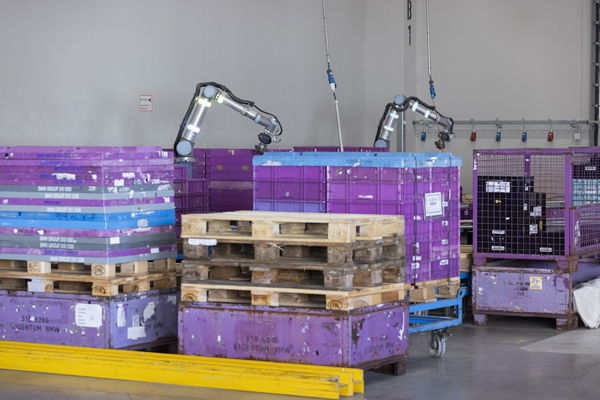
Robots, or automated systems, are used not just in some aspects of motorcycle assembly, but throughout the Logistics Centre as well. ‘Automated Guided Vehicles’ (AGVs) move components around in three areas of the logistics building while Small Transport Robots (STRs), as developed by BMW themselves, pick up parts and deliver them to the distribution points. ‘Trains’ of these vehicles also transport components in bulk. Even at the last, final station of the logistics centre, known as ‘Empties’, a robot system is used to identify, sort and stack empty boxes onto pallets for re-use.
An engine every two minutes
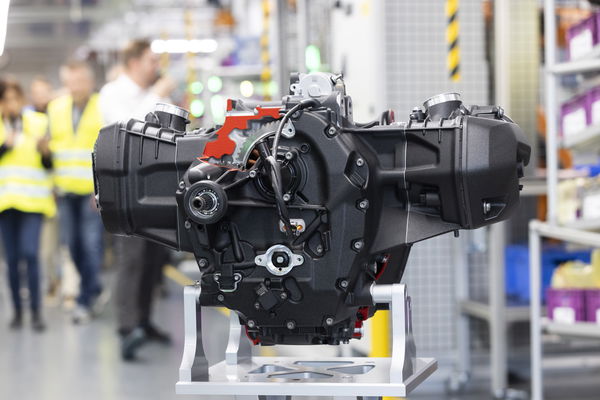
Motorcycle building starts with engine assembly. There are six engine assembly lines, five for petrol, one for electric with around 50 dedicated workers. There are also 21 robots involved in engine handling which helps keep the area compact with a high output. It takes two hours to assemble one engine, including repeated testing stations. One engine is produced every two minutes.
Final assembly (pic 10)
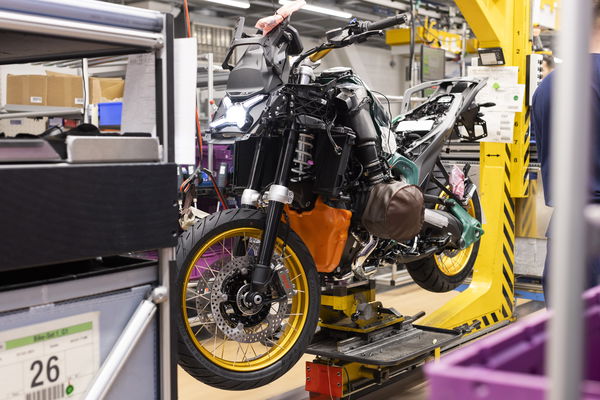
With engines complete it’s time for final assembly on, this time, four assembly lines. With parts of the engine protected by covers, the main frame is attached, then the swingarm, suspension, handlebars, controls, wheels and so on before fluids are added and the completed bike rolled off, first for a dyno test, then for final checks on a rolling road. Up to 800 different parameters are checked at up to 120kmh/75mph, which is why all new BMWs have 2-3km (or miles equivalent) on their odometers when delivered!